Understanding the Purpose and Proper Use of Vapor Barriers in Building Envelopes
Introduction
Moisture is one of the most insidious enemies of buildings—silent, unseen, and capable of wreaking havoc on insulation, framing, and indoor air quality. A vapor barrier (or vapor retarder) is your primary line of defense, installed within walls, ceilings, or floors to control the flow of water vapor and prevent condensation. In this detailed guide, we’ll dive into the science of moisture movement, explore how vapor barriers work, examine best practices for installation across climate zones, and share expert tips to ensure your building stays dry, comfortable, and durable for decades.
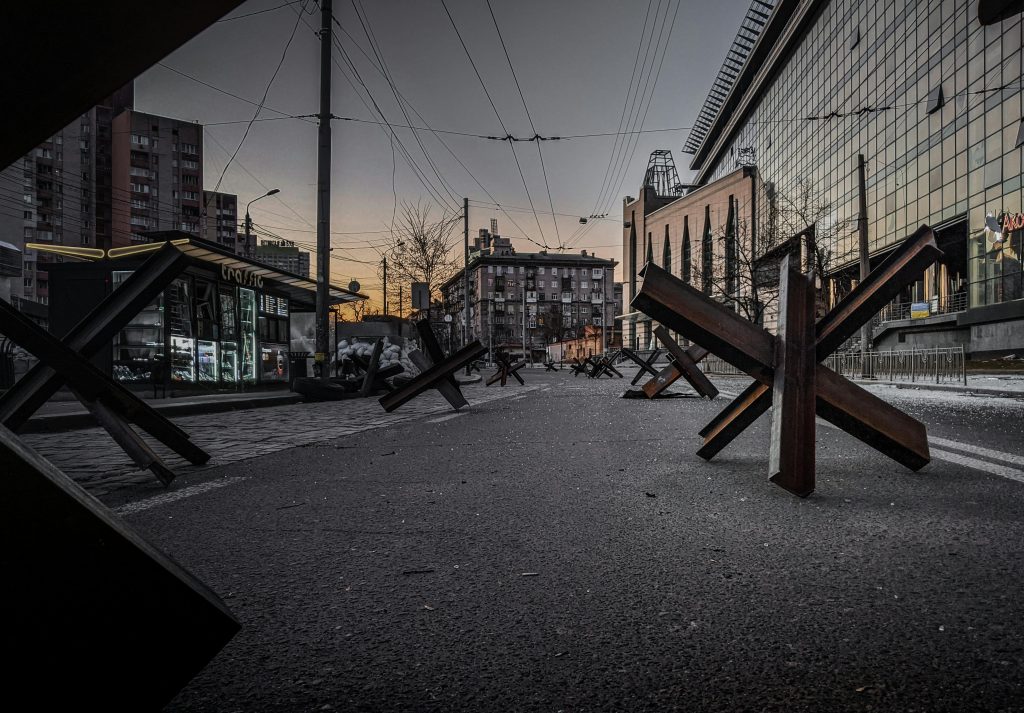
How Moisture Moves Through Building Assemblies
Diffusion vs. Air Leakage
- Diffusion (Vapor Drive): Water molecules in humid air migrate through porous materials—from warm to cold—driven by vapor-pressure differences.
- Air Leakage: Bulk airflow carries moisture-laden air through gaps, cracks, and vents; this is often the dominant moisture transport mechanism in leaky buildings.
Expert Insight: While caulking and weatherstripping address air leaks, vapor barriers target diffusion—two complementary strategies for a high-performance envelope.
The Condensation Problem
- Dew Point: As warm, moist air encounters a colder surface (e.g., exterior sheathing in winter), it cools to its dew point and condenses into liquid water.
- Consequence: Condensation trapped inside wall cavities leads to mold growth, wood rot, metal corrosion, and degraded insulation performance.
What Is a Vapor Barrier?
Definition and Materials
- A vapor barrier is a continuous layer of material that dramatically slows or prevents water vapor diffusion.
- Common Materials:
- Polyethylene sheeting (6 mil or thicker)
- Foil-faced kraft paper (on insulation batts)
- Coated gypsum or specialized vapor-retarder paints
Permeance Ratings (“Perms”)
- Class I (≤0.1 perm): True barriers (e.g., plastic sheeting, foil).
- Class II (0.1–1.0 perm): Moderate retarders (e.g., kraft-faced insulation).
- Class III (1–10 perms): Light retarders (e.g., certain paints).
Tip: Higher perm ratings allow more drying; choose the right class for your climate.
Where and How to Install Vapor Barriers
Climate Zone Strategies
- Cold Climates (Zones 5–8):
- Vapor barrier on the interior (warm side) of insulation to stop indoor moisture migrating outward.
- Mixed-Humid Climates (Zones 3–4):
- Use a Class II retarder or smart vapor barrier that adapts permeability with humidity.
- Hot-Humid Climates (Zones 1–2):
- Avoid interior barriers; focus on exterior drainage planes and allow walls to dry to the inside.
- Hot-Dry Climates:
- Vapor barriers are optional; moisture drive is minimal.
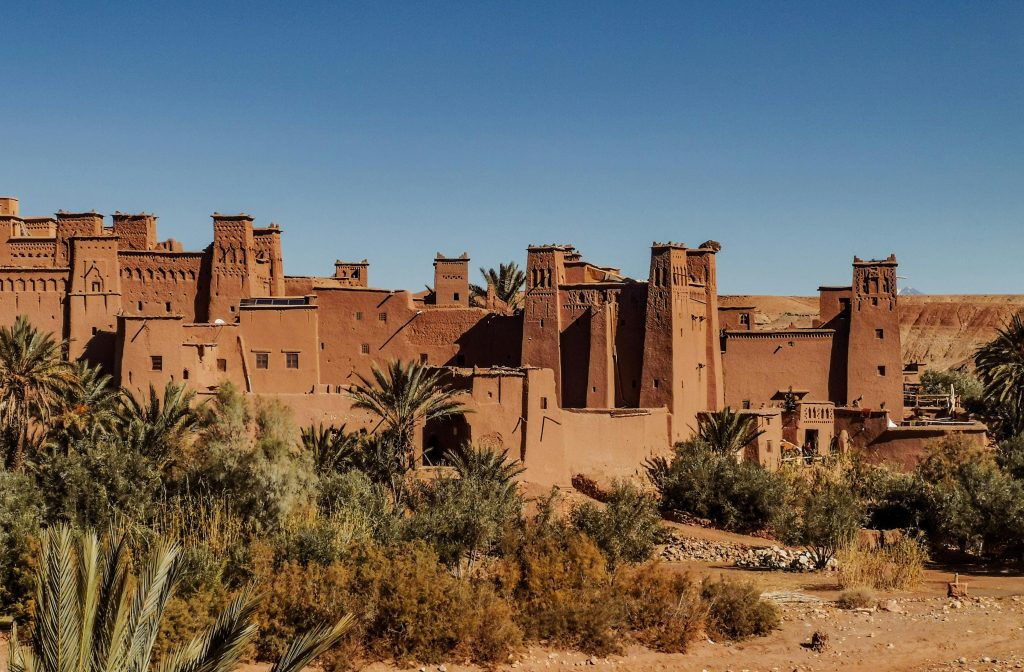
Installation Best Practices
- Continuous Coverage: Seal all seams with compatible tape; overlap by 6–12 inches.
- Edge Sealing: Tape to framing members, electrical boxes, and plumbing penetrations.
- Avoid Double Barriers: Two impermeable layers trap moisture; ensure at least one drying path.
- Integration with Air Barrier: Combine vapor and air barriers (e.g., sealed polyethylene) for maximum control.
textCopyEditWall Assembly Example (Cold Climate):
[Interior Finish]
Vapor Barrier (6 mil poly)
Insulation
Air Barrier (sealed sheathing)
Structural Sheathing
Exterior Cladding
Common Pitfalls and How to Avoid Them
Pitfall 1: Misplaced Vapor Barrier
- Symptom: Moisture condenses on the wrong side of the barrier.
- Solution: Analyze vapor drives in your climate; barrier always on the warm side of insulation.
Pitfall 2: Incomplete Sealing
- Symptom: Localized mold or damp spots near penetrations.
- Solution: Meticulously seal all edges, electrical boxes, pipes, and recessed lights.
Pitfall 3: Over-Reliance on Vapor Barriers
- Symptom: Walls that stay damp due to trapped moisture from construction or leaks.
- Solution: Combine with proper flashing, drainage planes, and controlled ventilation to allow drying.
Integrating Vapor Barriers with Other Moisture-Control Strategies
1. Air Barriers
- Role: Prevent bulk airflow (and moisture transport) through the envelope.
- Materials: House wraps (e.g., Tyvek), sealed gypsum, spray-applied membranes.
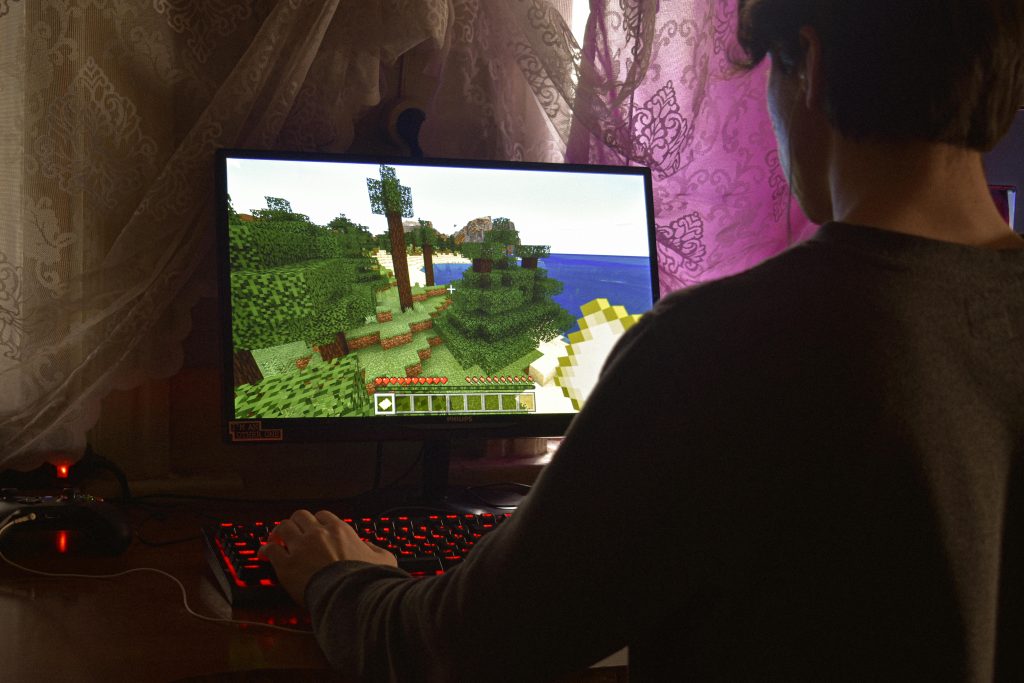
2. Drainage Planes
- Role: Redirect liquid water (rain, leaks) away from the sheathing.
- Components: Flashing, gap-created rainscreen, weep holes.
3. Ventilation and Drying
- Balanced Ventilation: ERVs or HRVs control indoor humidity, reducing vapor drive.
- Component Drying: Ensure walls can dry to at least one side—choose breathable claddings or retarders accordingly.
Real-World Example: Retrofitting an Attic
- Identify Problem: Ice dams and attic mold in a 40-year-old home.
- Air Sealing: Caulk and spray-foam attic floor to block convective air leaks.
- Vapor Retarder: Apply Class III vapor-retarder paint on the ceiling drywall.
- Attic Ventilation: Install ridge vents and soffit intakes to flush moisture.
Result: Condensation eliminated, mold cleared, and energy bills dropped by 15%.
Conclusion
A correctly specified and installed vapor barrier is a linchpin in a moisture-managed building envelope. By controlling water vapor diffusion, preventing condensation, preserving insulation performance, and enhancing durability, vapor barriers safeguard both structure and indoor air quality. The key is context: choose the right class of barrier, place it on the warm side of insulation, integrate it with air and drainage strategies, and ensure continuous, airtight installation. With these best practices, you’ll build—or retrofit—spaces that stay dry, healthy, and energy-efficient for generations.
Post Comment