Steel Framing vs Timber Framing: Key Differences and Best Uses
Introduction
Choosing the right framing system is foundational to any building project—from single-family homes to commercial towers. Steel framing and timber framing each bring unique strengths, challenges, and aesthetic qualities that directly impact cost, sustainability, and long-term performance. In this comprehensive guide, we’ll explore how these two popular structural systems differ in material properties, construction methods, environmental footprint, and more. By understanding their distinct advantages and limitations, you’ll be empowered to select the optimal framing solution for your next project.
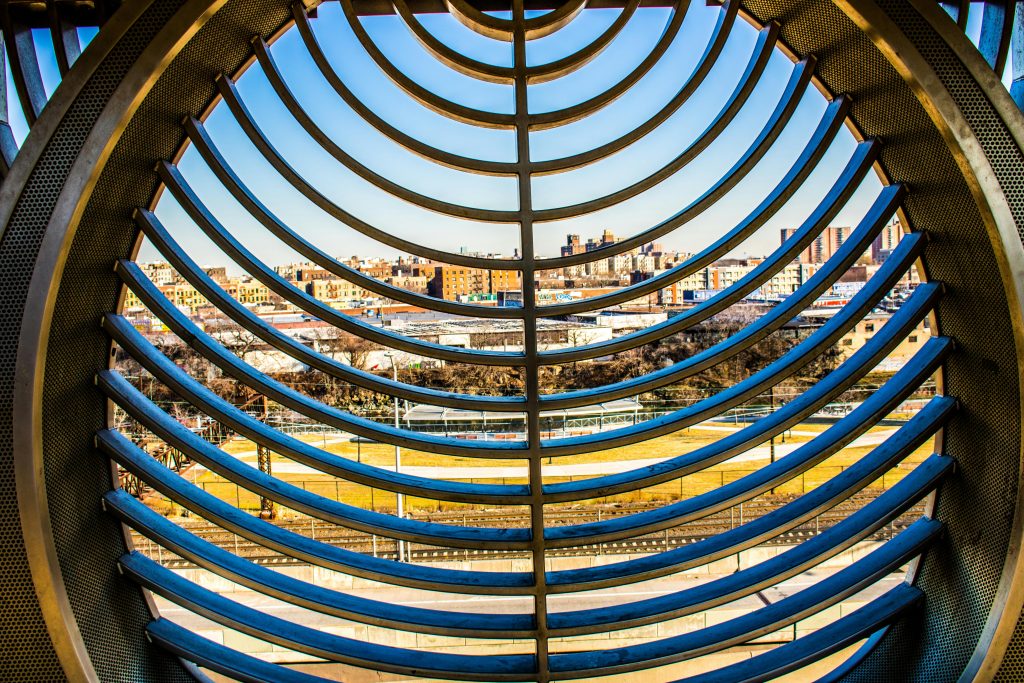
1. Material Properties and Structural Performance
1.1 Steel’s Strength and Consistency
- High tensile strength: Steel can handle heavy loads and long spans without excessive size.
- Dimensional stability: Unlike wood, steel won’t warp, twist, or shrink over time.
- Uniform quality: Manufactured in controlled conditions, each section meets precise tolerances.
1.2 Timber’s Natural Resilience and Flexibility
- Good compressive strength: Wood performs well under vertical loads, making it ideal for floor joists and studs.
- Energy absorption: Timber can flex slightly under stress, providing natural damping in seismic zones.
- Variable quality: Natural growth patterns introduce variability; quality depends on species, grade, and moisture content.
2. Design Flexibility and Architectural Applications
2.1 Steel for Bold, Open Concepts
- Longer clear spans: Perfect for wide-open spaces like warehouses, auditoriums, and modern lofts.
- Slimmer profiles: Steel members can be thinner than timber for the same load, maximizing interior space.
- Complex geometries: Easily formed into curves, angles, and hybrid assemblies.
2.2 Timber for Warmth and Tradition
- Rich aesthetics: Exposed timber beams evoke a sense of warmth and craftsmanship.
- Traditional joinery: Timber framing techniques—mortise and tenon, dovetails—add character.
- Mass timber innovations: Cross-laminated timber (CLT) panels now allow timber construction up to eight stories or more.
3. Construction Process and Speed
- Prefabrication:
- Steel: Sections cut and drilled in factory; on-site assembly with bolted connections.
- Timber: Panels and trusses can be factory-built, but custom cuts often require more on-site carpentry.
- Erection speed:
- Steel: Rapid erection cranes can assemble a steel frame in days for mid-rise buildings.
- Timber: Smaller crews can install panels and joists quickly on residential projects, but complex joinery may slow progress.
- Labor skills:
- Steel: Requires certified welders and crane operators.
- Timber: Skilled carpenters familiar with joinery and wood modifications.
4. Cost Considerations
4.1 Initial Material and Installation Costs
- Steel framing:
- Material costs are higher per linear foot compared to common framing lumber.
- Savings in labor time can offset some of the material expense.
- Timber framing:
- Lower raw-material cost in many regions.
- Labor can be more intensive if custom milling or joinery is involved.
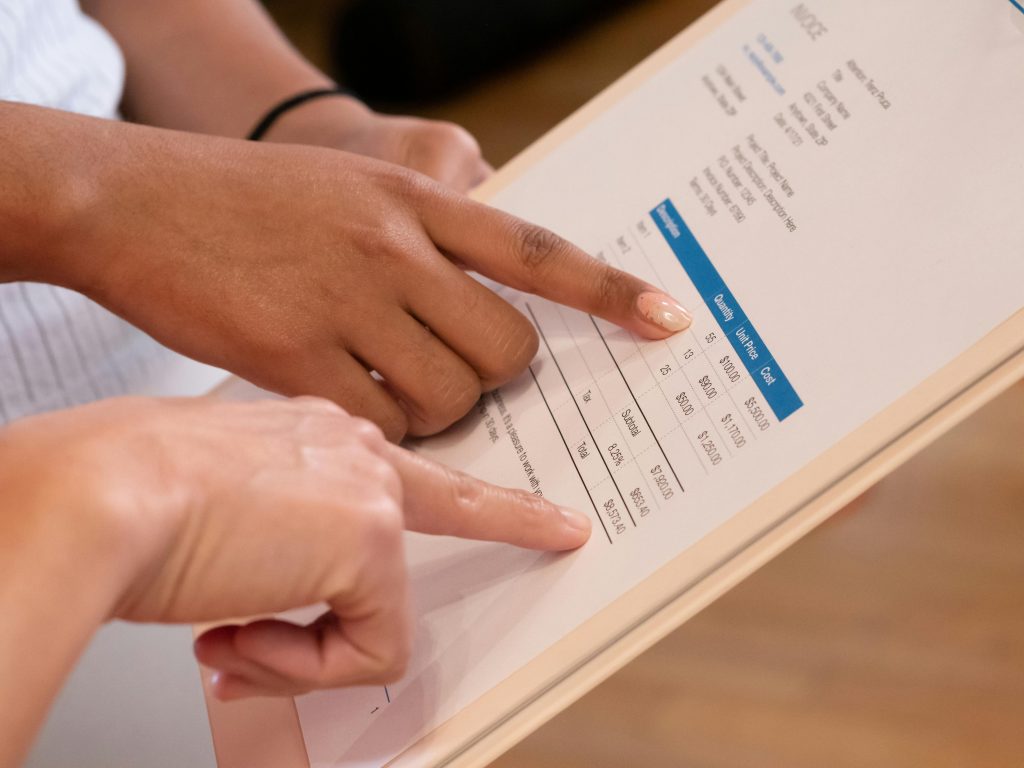
4.2 Lifecycle and Maintenance Expenses
- Steel:
- Resistant to rot, termites, and mold—lower long-term maintenance.
- Requires protective coatings to prevent corrosion.
- Timber:
- Periodic treatments against pests and moisture may be necessary.
- Can be refinished or repaired locally without full replacement.
5. Environmental Impact and Sustainability
- Embodied Energy:
- Steel: High energy input during production (smelting and rolling).
- Timber: Low embodied energy; trees sequester carbon as they grow.
- Carbon Footprint:
- Steel: Recycling reduces but does not eliminate emissions.
- Timber: Renewable resource; sustainably managed forests can be carbon-neutral or negative.
- End-of-life:
- Steel: 100% recyclable into new steel products.
- Timber: Can be reused, chipped for biomass, or composted—biodegradable.
6. Fire Resistance and Safety
6.1 Steel Behavior in Fire
- Loss of strength: Above 550 °C, steel can lose up to 50% of its load capacity.
- Fireproofing required: Intumescent coatings or fire-rated enclosures add cost and thickness.
6.2 Timber Fire Performance
- Charring effect: Mass timber chars on the outside, slowing heat penetration and preserving core strength.
- Natural fire resistance: Heavy-timber members often meet one- to two-hour fire-rating without additional protection.
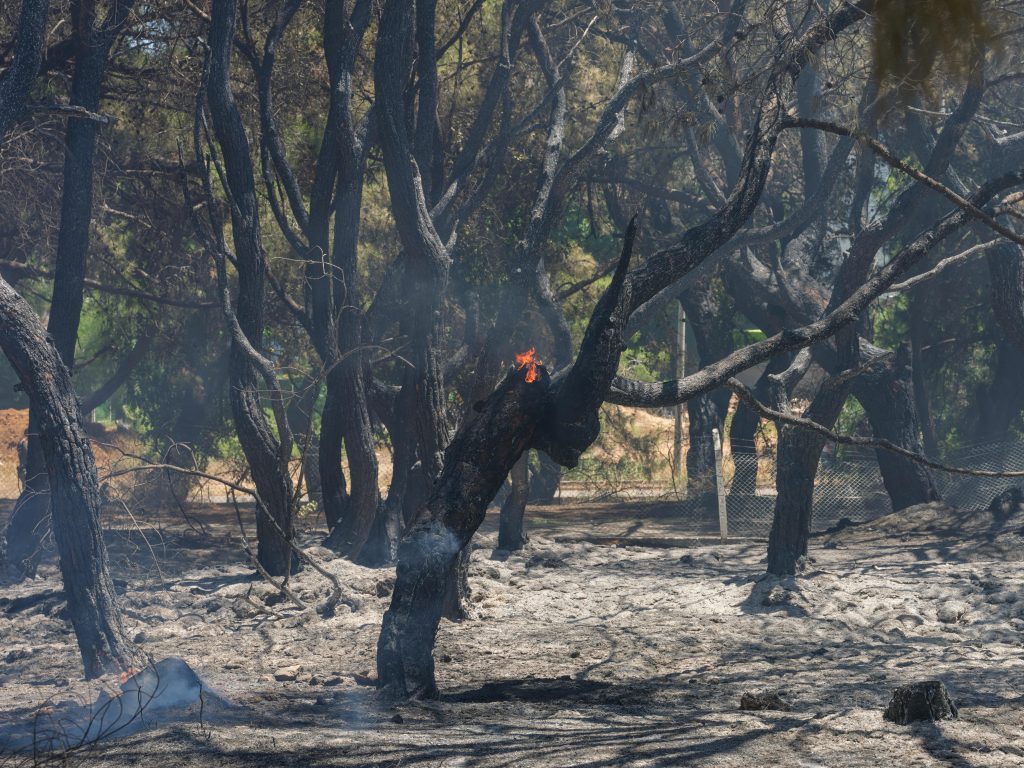
7. Acoustic and Thermal Performance
- Thermal Bridging:
- Steel studs: High conductivity creates cold bridges—requires thermal breaks or insulation strategies.
- Timber studs: Lower conductivity, better baseline thermal performance.
- Sound Transmission:
- Steel framing: May transmit vibration; resilient channels and insulation can mitigate noise.
- Timber framing: Natural damping reduces airborne and impact sound with less auxiliary treatment.
8. Regulatory and Code Implications
- Building Codes:
- Both systems are well covered in international and local codes (e.g., IBC, Eurocode, NBC).
- Steel often requires additional seismic bracing in high-risk zones.
- Insurance & Permitting:
- Timber structures may face higher fire-insurance premiums in wildland-urban interface areas.
- Steel projects might require specialized inspections for welds and bolted connections.
9. Real-World Case Studies
9.1 Commercial Warehouse: Steel Advantage
- Project: 150,000 ft² logistics hub
- Result: 80 ft clear spans enabled by wide-flange beams, erected in four weeks.
- Benefit: Minimal internal columns maximize storage efficiency.
9.2 Residential Retreat: Timber’s Charm
- Project: 2,500 ft² vacation home in a forest setting
- Result: Exposed glulam beams and CLT floors create a cozy, natural interior.
- Benefit: Earned a LEED Gold rating for low embodied carbon and sustainable forestry.
10. Choosing the Right Option for Your Project
Ask yourself:
- Structural Requirements: Do you need long spans or heavy load capacity?
- Budget Constraints: What balance between material vs. labor costs works for you?
- Aesthetic Goals: Are you aiming for a modern industrial look or a warm, natural interior?
- Sustainability Targets: Is low carbon footprint a priority?
- Local Expertise: Do local contractors specialize in steel or timber?
- Code & Insurance: What are the regulatory and insurance implications in your region?
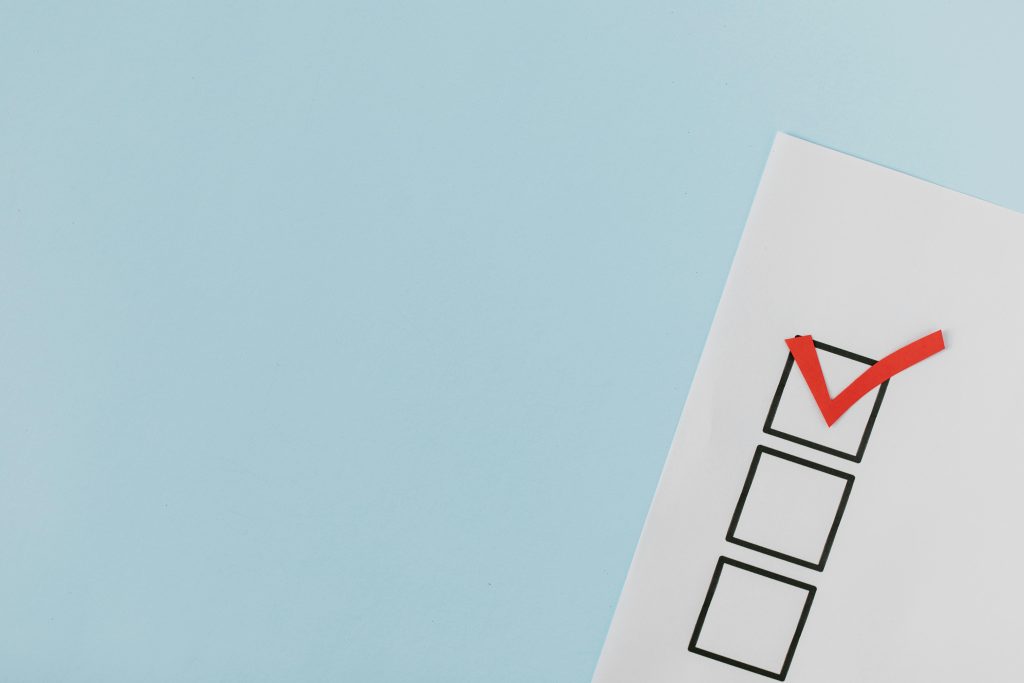
Conclusion
Steel framing and timber framing both offer compelling benefits—whether you prioritize strength, speed, sustainability, or aesthetic warmth. By weighing material properties, construction processes, cost factors, and environmental impacts, you can align your project goals with the most suitable structural system. In many cases, hybrid approaches (e.g., steel-timber composite panels) unlock the best of both worlds. Armed with these insights, you’re ready to make an informed framing choice that stands the test of time, budget, and design ambition.
Post Comment