How Moisture Content Affects Timber Strength: A Comprehensive Guide
Wood’s natural beauty, versatility, and renewability make it a popular choice for everything from structural beams to handcrafted furniture. Yet timber is also a living material that constantly exchanges water with its surroundings. That moisture content (MC) profoundly influences how strong, stiff, and stable wood performs in real-world applications. In this in-depth post, you’ll learn the science of how water interacts with wood fibers, discover why strength drops as moisture rises below the fiber-saturation point, explore practical drying and design strategies, and see real-life examples that illustrate best practices. By the end, you’ll have a detailed toolkit for specifying, installing, and maintaining timber structures and products that stand the test of time.
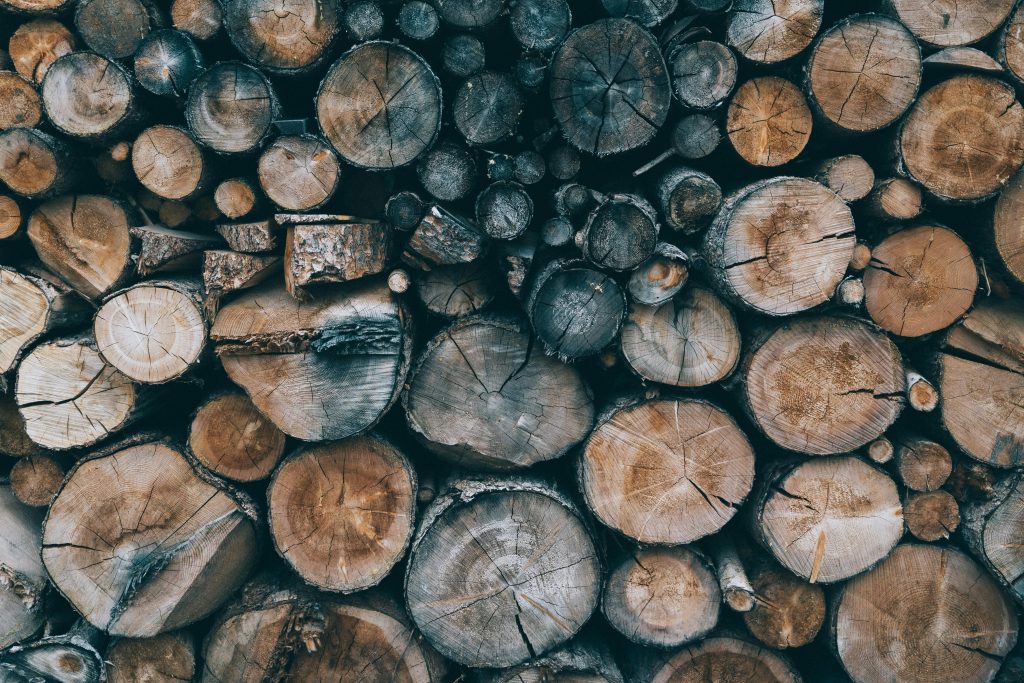
Understanding Moisture Content and the Fiber-Saturation Point
Moisture Content (MC) expresses the percentage of water in wood relative to its oven-dry mass:
plaintextCopyEditMC (%) = (mass of water in wood ÷ oven-dry mass of wood) × 100
Wood holds water in two forms:
- Bound water within the cell-wall polymers
- Free water inside cell lumens (cavities)
The Fiber-Saturation Point (FSP)—typically around 25–30% MC—marks the threshold where cell walls are fully saturated, but lumens contain no free water. Below this point, water acts as a plasticizer, weakening cell-wall bonds. Above it, additional water resides in lumens, with little further effect on mechanical properties.
How Moisture Content Influences Mechanical Properties
Strength Reduction Below the FSP
As MC climbs from 0% toward the FSP, key strength parameters decline roughly linearly:
- Bending Strength (Modulus of Rupture, MOR): decreases by about 3% per 1% MC increase
- Compression Parallel to Grain: drops 2% per 1% MC
- Tensile Strength Parallel to Grain: falls 1% per 1% MC
- Stiffness (Modulus of Elasticity, MOE): reduces 1% per 1% MC
Real-World Analogy: Imagine a dry rubber band that becomes more stretchy when damp—wood fibers similarly soften when bound water disrupts intermolecular bonds.
Plateau of Properties Above the FSP
Once free water appears in lumens (MC > FSP), mechanical properties stabilize:
- No Further Weakening: Wood at 50% MC is no weaker than at 30% MC.
- Implication for Green Timber: Freshly cut logs (often 80–200% MC) share the same strength as wood just at FSP, so drying below 30% yields the most significant gains.
Quantifying Strength Variation
The table below summarizes approximate relative strength values for typical softwoods. Actual figures vary by species and testing methods:
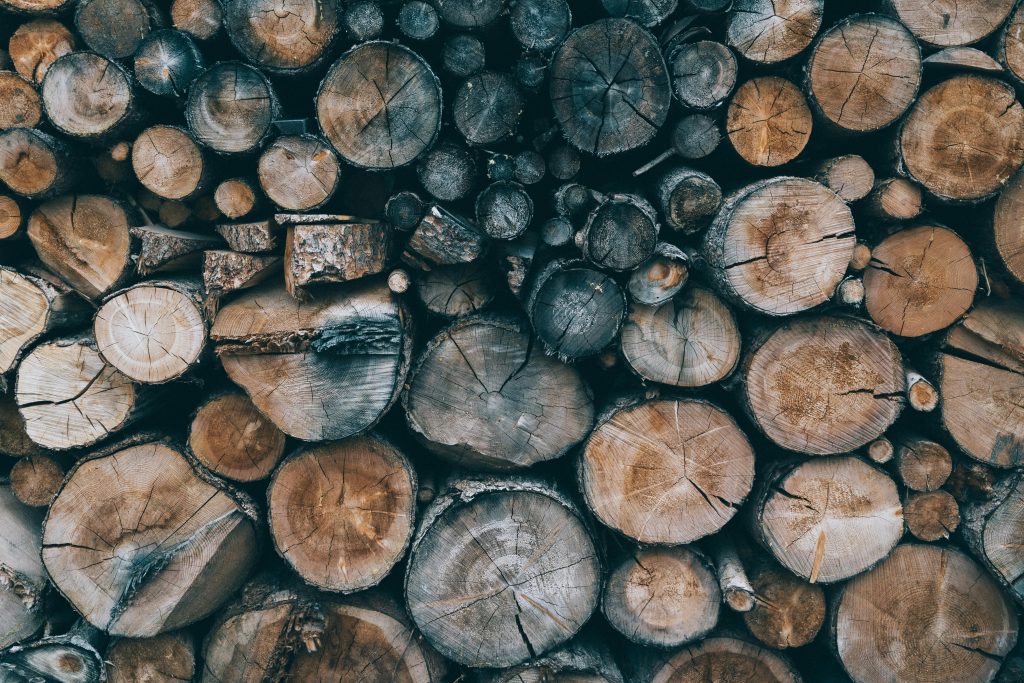
MC (%) | Relative MOR (%) | Relative MOE (%) | Relative Compression Strength (%) |
---|---|---|---|
0 | 100 | 100 | 100 |
6 | 88 | 92 | 94 |
12 | 76 | 84 | 88 |
20 | 64 | 76 | 80 |
30 | 55 | 70 | 72 |
Note: For hardwoods, percentage declines can be steeper; always consult species-specific data for critical applications.
Drying Methods and Target Moisture Levels
Air Drying vs. Kiln Drying
- Air Drying:
- Economical, uses natural airflow and seasonal conditions
- Requires 6–24 months; uneven moisture gradients can cause checking
- Kiln Drying:
- Controlled environment regulates temperature, humidity, and airflow
- Completes in days or weeks; minimizes defects if properly managed
Recommended Target MC
Application | Target MC (%) |
---|---|
Interior Structural Framing | 8–12 |
Exterior Decking & Cladding | 12–18 |
Furniture & Millwork | 6–10 |
Tip: After delivery, acclimatize lumber on-site (48–72 hours) to let surface moisture equalize with local conditions before installation.
Designing for Moisture-Induced Movement
Wood shrinks and swells mostly across the grain as MC fluctuates:
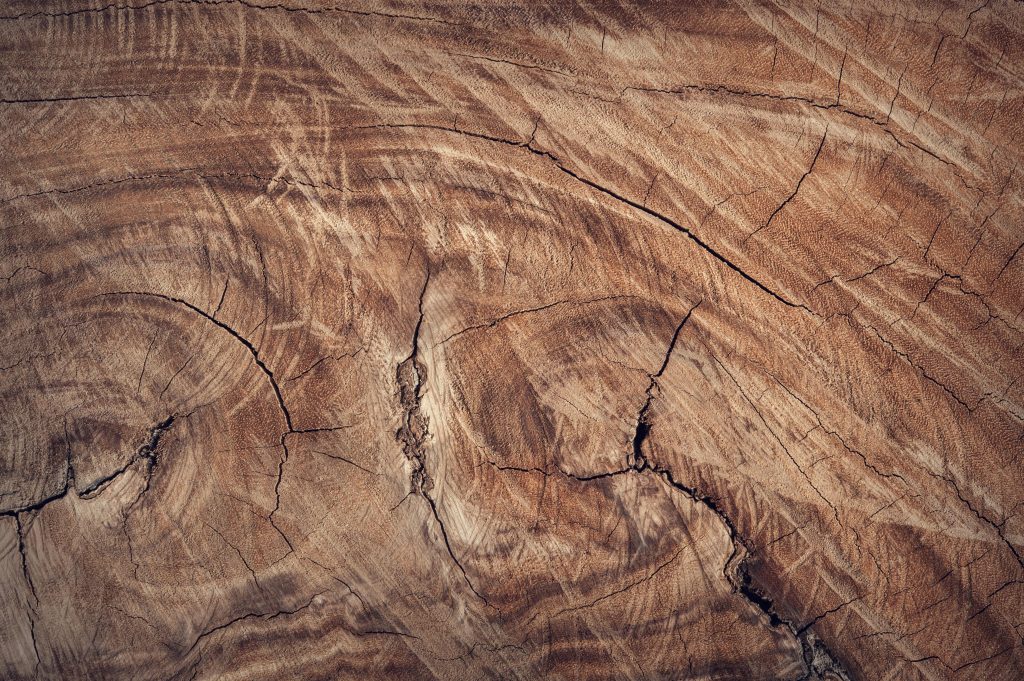
- Tangential Shrinkage (cross-grain): up to twice radial shrinkage
- Radial Shrinkage (along growth rings): smaller but still significant
- Total Green-to-Dry Shrinkage: often 6–12% in wider boards
Strategies for Building Resilience
- Movement Gaps:
- Leave 1–3 mm of space per 300 mm of board width for flooring, decking, or siding.
- Floating Assemblies:
- Use slotted screw holes or oversized fastener slots so boards can expand/contract.
- Staggered Joints:
- Avoid long runs of seamless boards; stagger end joints to reduce cumulative stress.
Example: In a hardwood floor, installing 150 mm wide planks with 2 mm side and end gaps allows for up to 8 mm seasonal expansion without buckling.
Equilibrium Moisture Content (EMC): The In-Service Reality
Once installed, wood migrates toward the EMC dictated by ambient relative humidity (RH) and temperature:
- Indoor EMC: typically 6–9% (40–60% RH at 20 °C)
- Outdoor EMC: 10–20% (climate-dependent)
Tools like the Hailwood-Horrobin equation can estimate EMC, but practical rule-of-thumb tables suffice for most building designs.
Applying Code and Safety Factors
Structural codes incorporate moisture effects via modification factors:
- Eurocode 5: Uses k_mod to adjust characteristic strength based on service class (1: indoor, 2: sheltered exterior, 3: unprotected exterior).
- NDS (North American): Tables provide allowable stresses for varying MC and species.
Practice: Always select the modified strength value corresponding to the worst-case in-service MC for your project’s service class.
Case Study: Exterior Deck Installation
Scenario: A homeowner in a humid climate (annual RH 70–90%) wants a cedar deck.
- Species Selection: Western red cedar—naturally lower EMC and good stability
- Drying Target: 12–15% MC for exterior boards
- Installation Details:
- 3 mm gaps between 125 mm boards (≈2.4 % width)
- Stainless-steel screws in slotted holes
- Joist spacing at 400 mm centers to reduce board deflection
- Outcome: Minimal cupping and checking over two years, with boards tracking ±3% width changes seasonally.
Best Practices for Builders and Engineers
- On-Site Moisture Monitoring: Use accurate pin or capacitive meters to verify MC before installation.
- Protect Storage Areas: Stack lumber on dry, level supports with stickers for airflow; cover but ventilate.
- Plan for Seasonal Swings: In regions with large RH shifts, anticipate ±4–6% MC variation between summer and winter.
- Regular Inspections: In high-humidity environments, check critical structural members annually and adjust ventilation or coatings as needed.
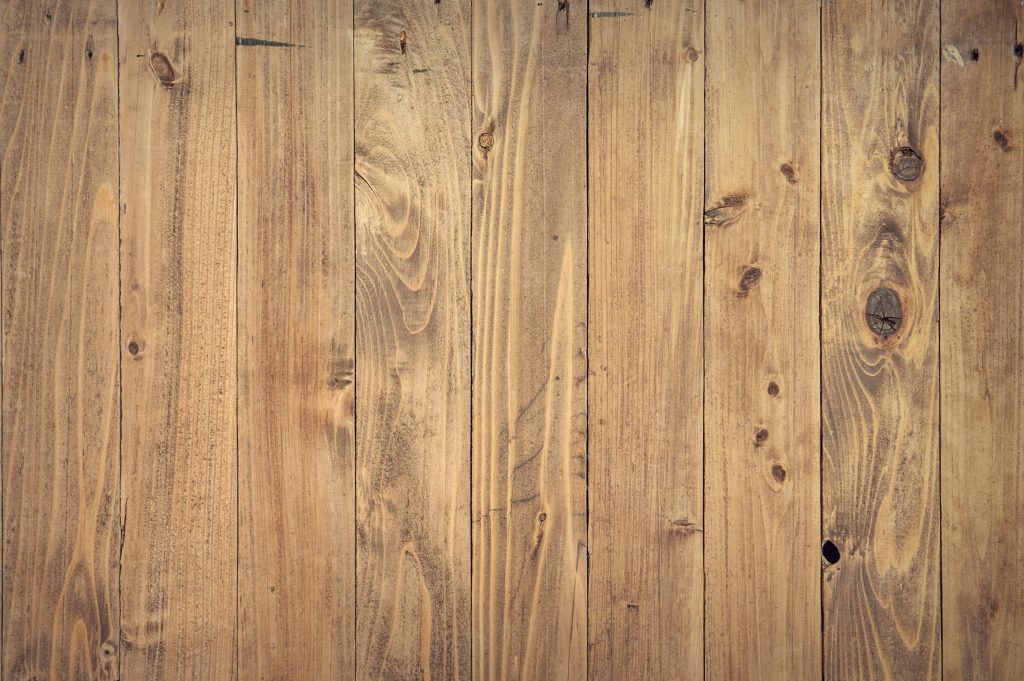
Conclusion
Timber’s hygroscopic nature demands respect and planning. Below the fiber-saturation point, each additional percent of bound water undermines strength and stiffness; beyond that, extra water in lumens has little further effect. By targeting appropriate drying levels, designing joints that accommodate shrinkage and swelling, applying code-mandated modification factors, and monitoring in-service moisture, you can harness wood’s strengths while avoiding moisture-related failures. Armed with these insights and strategies, architects, engineers, and builders can create wooden structures and products that remain safe, functional, and beautiful for decades to come.
Post Comment