How to Choose Between Plywood and OSB
Introduction
When it comes to structural sheathing, subfloors, roofing, and wall sheathing, builders and DIYers often face the same dilemma: should I use plywood or OSB (oriented strand board)? Both materials offer strength and affordability, but their unique properties make each better suited to certain applications. Choosing the right panel not only affects structural integrity but also budget, moisture resistance, and long-term performance. In this guide, we’ll compare plywood and OSB across multiple factors—strength, moisture resistance, cost, environmental impact, and ease of installation—and help you determine which is the best fit for your next project.
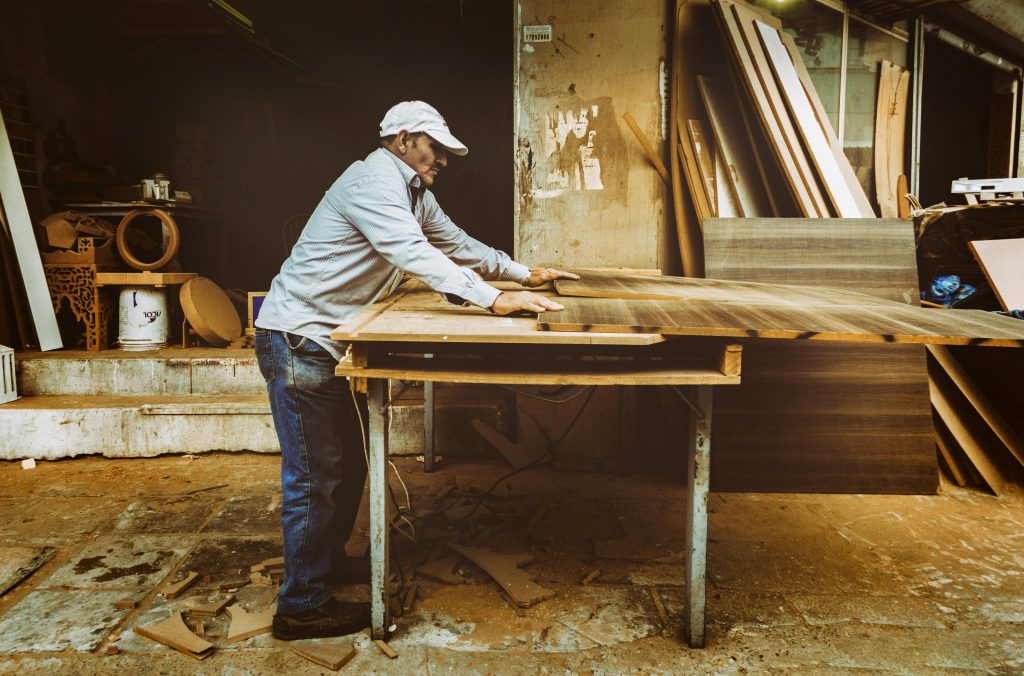
What Is Plywood?
Composition and Manufacturing
Plywood is made by gluing together thin layers (plies) of wood veneer, with adjacent layers’ grain running perpendicular. This cross-grain construction:
- Increases strength and dimensional stability
- Reduces warping and splitting
- Allows for consistent performance across the panel
Each ply is typically 1/8″ to 1/4″ thick, bonded with waterproof adhesive under heat and pressure. The number of plies varies with panel thickness; for example, a 3/4″ panel might have five or seven plies.
Grades and Face Veneers
Plywood comes in exterior and interior grades, each with lettered veneers:
- A grade: Smooth, paint-ready face with minimal defects
- B grade: Solid face with minor repairs or filling
- C and D grades: More knots and repairs; often used where appearance is less critical
For roof and wall sheathing, manufacturers typically use C-D Exterior or C-D Exposure 1, balancing cost and structural performance.
What Is OSB?
Composition and Manufacturing
Oriented strand board is engineered from thin wood strands (flakes) arranged in cross-oriented layers and bonded with waterproof resin under heat and pressure. Key characteristics:
- Strand orientation: Faces are aligned parallel to the panel’s long axis for strength; core layers run perpendicular.
- Flake size: Smaller than veneer plies, providing a uniform feel and reducing waste.
- Resin binding: Often phenol-formaldehyde or polymeric methylene diphenyl diisocyanate (pMDI) for water resistance.
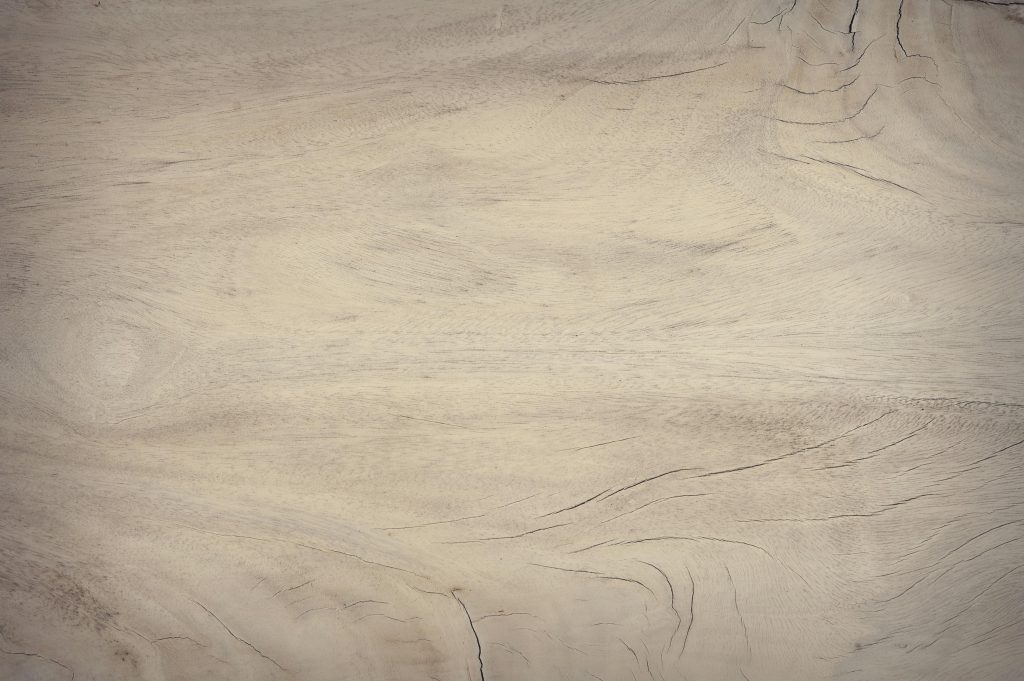
OSB panels are almost always Exposure 1 or Exposure 2 rated, indicating suitability for exterior sheathing when properly protected.
Standard Thickness and Sizes
Common OSB thicknesses mirror plywood (1/2″, 5/8″, 3/4″), but OSB panels often weigh more. Standard panel dimensions are 4’×8′, with options up to 4’×12′.
Strength and Structural Performance
Property | Plywood | OSB |
---|---|---|
Tensile (perpendicular) | Higher—less likely to sag between joists | Good, but slightly lower than plywood |
Racking resistance | Excellent—stiffer under shear loads | Very good; modern grades close plywood |
Edge bearing | Strong—better support along edges | Adequate, but edges prone to swell if wet |
Fastener withdrawal | Superior—holds nails and screws firmly | Slightly lower withdrawal strength |
- Span Rating: Both materials carry span ratings (e.g., 24/16 for roof sheathing), dictating maximum joist spacing. Always match panel rating to your application.
- Racking Performance: Plywood’s continuous veneer surfaces provide marginally higher shear stiffness, making it a top choice for shear walls and areas prone to high lateral loads (e.g., hurricane zones).
Moisture Resistance and Durability
Edge and Surface Swelling
- Plywood: Minimal swelling (2–5%) when exposed to moisture, due to dense veneers and exterior-grade adhesives.
- OSB: Higher swelling (8–15%) at edges if not sealed, because exposed strands absorb water more readily.
Long-Term Exposure
- Plywood: Better suited for intermittent wetting; less prone to delamination or rot if dried properly.
- OSB: Acceptable for sheathing when covered promptly by roofing or siding; prolonged exposure can lead to bulging and fungal growth along panel seams.
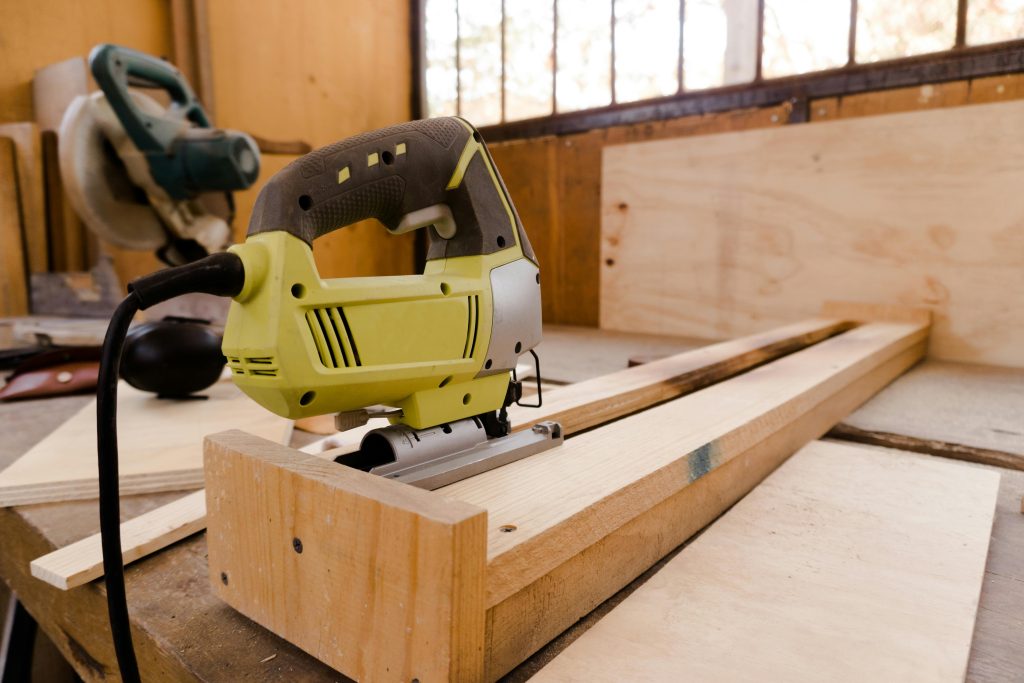
Best Practice: Seal cut edges of either panel with primer or compatible sealant to minimize moisture ingress. Grade-stamped OSB with “T&G” (tongue and groove) profiles can help limit water penetration at joints.
Cost Comparison
Panel Type | Approximate Cost per 4×8 Sheet¹ | Cost Factor |
---|---|---|
Plywood | $40 – $60 | Higher material and manufacturing costs |
OSB | $25 – $40 | Economical, made from fast-growing trees |
¹Prices vary by region, thickness, and market conditions.
- OSB often costs 30–40% less than plywood, making it the default for budget-conscious builders.
- When roof or wall sheathing covers thousands of square feet, the price difference can amount to thousands of dollars.
Environmental Impact
Resource Utilization
- Plywood: Uses hardwood or softwood veneers; quality logs required, leading to higher environmental footprint per panel.
- OSB: Utilizes small-diameter, fast-growing trees, including thinnings from forest management, making it more sustainable in terms of raw-material use.
Lifecycle and Recycling
- Plywood: Difficult to recycle due to adhesives; often ends up in landfills.
- OSB: Similarly challenging to recycle, though some manufacturers explore repurposing flakes into composite mats.
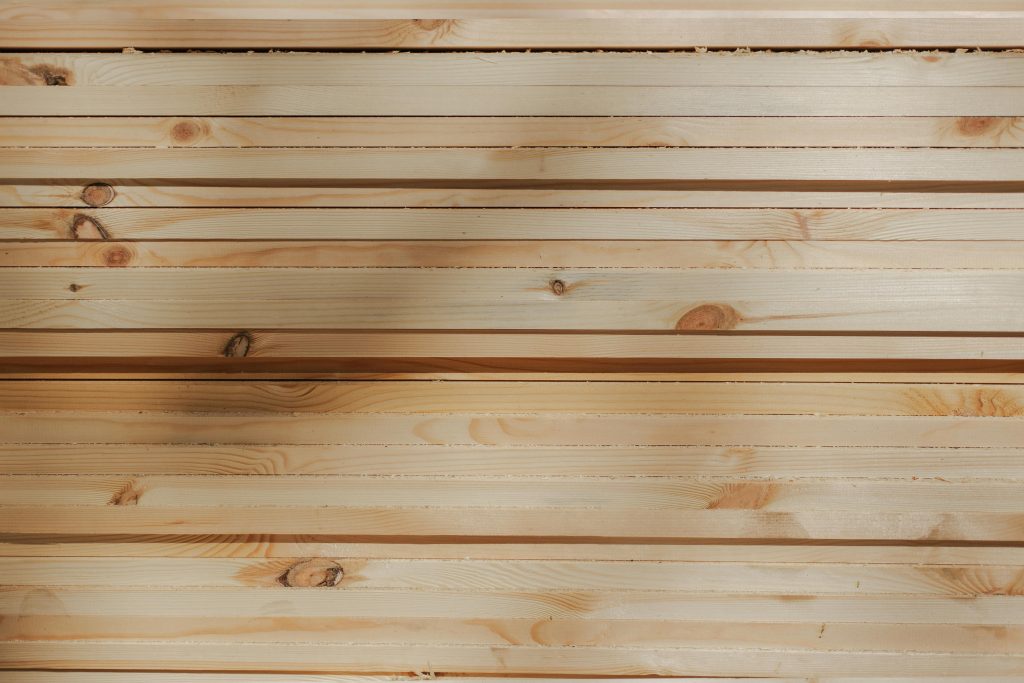
Green Tip: Look for panels certified by the Forest Stewardship Council (FSC) or Sustainable Forestry Initiative (SFI) to ensure responsible sourcing.
Application Scenarios
Roof Sheathing
- OSB dominates in modern construction for roof decks, thanks to cost savings and adequate strength.
- Plywood may be preferred in regions with heavy snowfall or high winds, where superior racking resistance and moisture tolerance offer extra safety.
Wall Sheathing
- OSB works well for conventional framing sheathing when covered by weather-resistant barriers.
- Plywood is chosen for shear walls or in high-seismic zones where code may require higher shear values.
Subflooring
- Plywood edges resist moisture from spills or subfloor heating; lower swelling preserves finish materials.
- OSB subfloor panels with tongue-and-groove edges are acceptable if glue and fasteners are applied per manufacturer instructions.
Cabinetry and Millwork
- Plywood is the standard for cabinets, shelving, and finish carpentry because it holds fasteners securely and has a smooth veneer suitable for veneers or laminates.
- OSB is rarely used for fine woodworking due to its rough surface and poor screw-holding at edges.
Installation Tips
- Fastening
- Use ring-shank nails or screws spaced per code: typically 6″ o.c. at panel edges, 12″ o.c. in the field.
- For subfloors, apply construction adhesive beneath each sheet to minimize squeaks.
- Panel Orientation
- Run panel strength axis perpendicular to framing members.
- Stagger joints between panels to increase shear continuity.
- Sealing and Flashing
- Apply roofing felt or house wrap immediately after sheathing.
- Prime all cut edges and drill holes before exposure to the elements.
- Acclimatization
- Store panels flat, off the ground, under cover for at least 48 hours to acclimate to ambient humidity.
- Avoid installing frozen or wet panels, which may buckle or warp as they dry.
Common Misconceptions
- “OSB and plywood are interchangeable.”
While both serve similar structural roles, their behaviors under moisture and load differ enough to influence choice. - “Plywood always outperforms OSB.”
Modern OSB grades meet or exceed code requirements for many applications; plywood’s advantages are incremental and context-dependent. - “Cost savings justify OSB everywhere.”
If your project demands high durability, edge stability, or finish quality, the premium for plywood can be cost-effective in the long run.
Making Your Decision
Consider the following questions:
- What’s the application? Roofing, walls, subfloors, or finish work?
- What are your climate and exposure conditions? High humidity, rainfall, snow load, or coastal salt spray?
- What’s your budget? How much square footage are you covering?
- Do you need superior screw-holding or shear performance?
- Are you aiming for sustainability certifications?
Answering these helps you weigh performance against cost and environmental factors to choose the optimal panel for each use.
Conclusion
Both plywood and OSB have distinct advantages. OSB often wins on price and sustainability of raw materials, making it the go-to for large-scale sheathing projects in temperate conditions. Plywood offers superior moisture resistance, fastener holding, and shear stiffness—ideal for critical structural components, high-exposure environments, and finish applications. By understanding each panel’s properties, matching them to your project’s demands, and following best installation practices, you can ensure a durable, cost-effective build that stands the test of time.
Post Comment