What Are Expansion Joints and Why Are They Necessary?
Introduction
Expansion joints are critical yet often overlooked components in buildings, bridges, roads, and piping systems. They serve as engineered gaps or flexible connections that absorb dimensional changes caused by temperature fluctuations, moisture, vibration, and seismic activity. Without properly designed expansion joints, structures are vulnerable to cracking, warping, or catastrophic failure. In this post, we’ll explore the fundamentals of expansion joints, the different types used across industries, and the engineering principles that make them indispensable for safety and longevity.
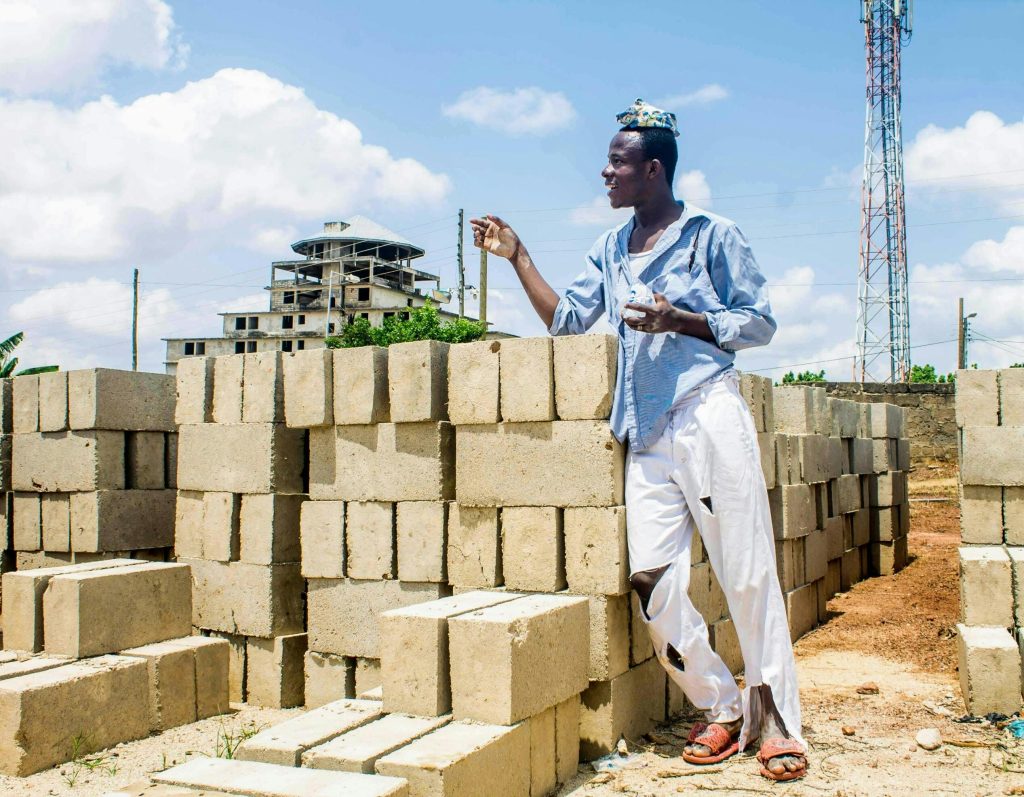
Main Body
1. The Science Behind Expansion and Contraction
Every material—whether steel, concrete, asphalt, or plastic—expands when heated and contracts when cooled. This thermal movement is quantified by the coefficient of thermal expansion (CTE), typically expressed in microstrains per degree Celsius (µε/°C).
- Example: Concrete has a CTE around 10 µε/°C; a 30 m concrete slab exposed to a 30 °C temperature swing could change length by nearly 9 mm!
Uncontrolled movement leads to high stresses, which manifest as:
- Cracks and spalling in concrete.
- Buckling or warping of road surfaces.
- Leaks in pipelines and ductwork.
Expansion joints accommodate this movement, relieving stress and preserving structural integrity.
2. Common Applications of Expansion Joints
2.1 Buildings and Structures
- Façade Joints: Placed between precast panels or curtain-wall segments to prevent cracks and water infiltration.
- Floor Joints: In large halls, malls, or warehouses; allow slab movement over long spans.
- Roof Joints: Compensate for thermal uplift and building sway.
2.2 Bridges and Highways
- Bridge Deck Joints: Typically modular elastomeric bearings or finger joints that handle vertical loads and horizontal displacement.
- Roadway Joints: Saw-cut or preformed filler strips placed in pavements to control cracking.
2.3 Pipelines and Ductwork
- Bellows Expansion Joints: Corrugated metal assemblies that flex under thermal cycling and pressure changes.
- Slip-Type Joints: Allow axial movement by sliding telescoping sections.
2.4 Rail and Transit Systems
- Rail Expansion Gaps: Small gaps between rail segments prevent buckling under heat.
- Platform Joints: Enable safe boarding while accommodating structural movement.
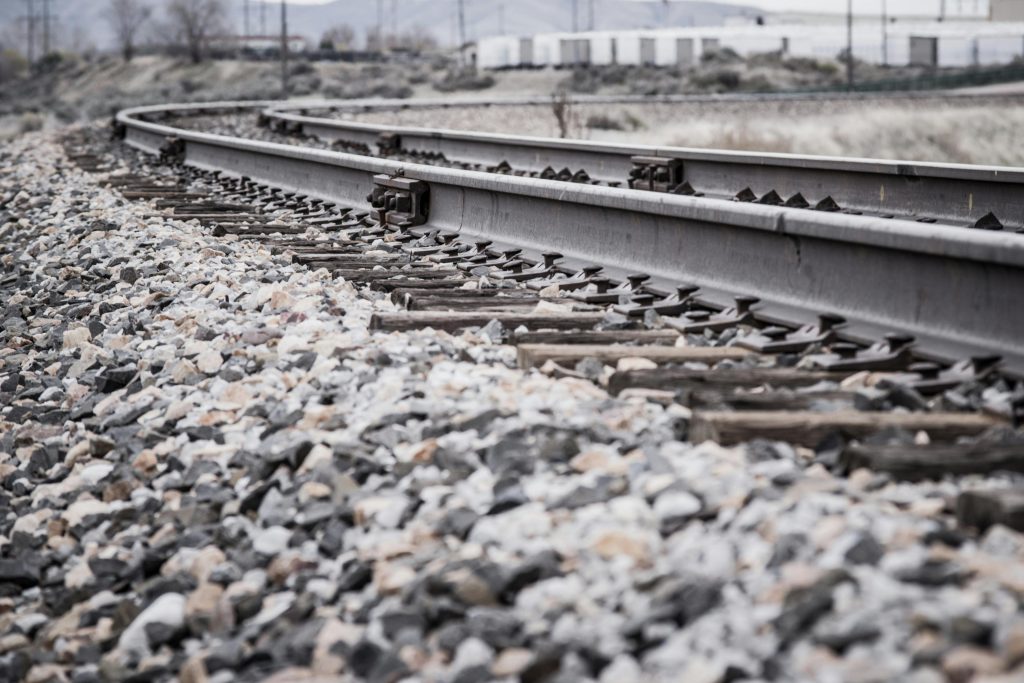
3. Types of Expansion Joints
Type | Description | Typical Movement Accommodated |
---|---|---|
Butt Joint | Simple gap with filler material (foam, cork, rubber) | Small thermal movements; moisture sealing |
Finger Joint | Interlocking metal “fingers” that span a gap | Large horizontal and vertical movements (e.g., bridges) |
Bellows Joint | Corrugated metal or rubber assembly | High pressure, multi-axis movement (piping, HVAC) |
Sliding Joint | Telescoping sections with sliding plates or bearings | Axial movements; moderate pressure applications |
U-Type Joint | U-shaped bellows for large offsets | Lateral, axial, and angular movements |
4. Design Considerations
When specifying an expansion joint, engineers evaluate:
- Magnitude of Movement: Based on temperature range, moisture changes, and seismic codes.
- Type of Movement: Axial (lengthwise), lateral (sideways), or angular (rotational).
- Load Requirements: Static and dynamic loads, pressure in pipelines, foot traffic.
- Durability and Maintenance: Material compatibility, fatigue life under cyclic loading, ease of inspection.
- Sealing and Water-Tightness: Especially important in façades and below-grade applications.
Real-World Analogy: Think of expansion joints like the accordion bellows in an old camera—flexible folds that let the camera extend without straining the frame.
5. Materials Used in Expansion Joints
- Elastomers (Rubber, Neoprene): Good for low-pressure, large-deformation applications (e.g., building joints, sidewalks).
- Metal Bellows (Stainless Steel, Monel): Ideal for high-temperature or high-pressure piping.
- Foam and Cork: Used as backer rods in simple butt joints to support sealants.
- Thermoplastics (PTFE): Resistant to chemicals, used in corrosive environments.
6. Installation Best Practices
- Proper Sizing: Ensure joint width and depth accommodate expected movement plus sealant thickness.
- Clean Substrate: Remove dust, oil, and old caulk for optimal adhesion.
- Backer Rod Placement: Install a compressible backer rod to control sealant depth and bond lines.
- Sealant Application: Use compatible, movement-rated sealants—apply too thin, and it tears; too thick, and it sags.
- Inspection and Maintenance: Regularly check for sealant degradation, joint misalignment, or fatigue cracks.
7. Case Study: Bridge Deck Expansion Joint Failure
In 2018, a metropolitan bridge experienced premature deck joint failure due to understating temperature swings and selecting a rigid finger joint unsuited for high traffic loads. Cracking led to water infiltration, corroding the reinforcement and requiring emergency repairs. Retrofitting with a wider modular elastomeric bearing resolved movements up to 50 mm and extended service life by decades.
8. Benefits of Proper Expansion Joint Design
- Extended Service Life: Mitigates stress concentrations that cause early failure.
- Improved Safety: Prevents tripping hazards in pavements and maintains structural stability in seismic zones.
- Lower Maintenance Costs: Reduces frequency of crack repairs and downtime.
- Enhanced Performance: Maintains watertight seals in façades and pipelines, preventing leaks and energy loss.
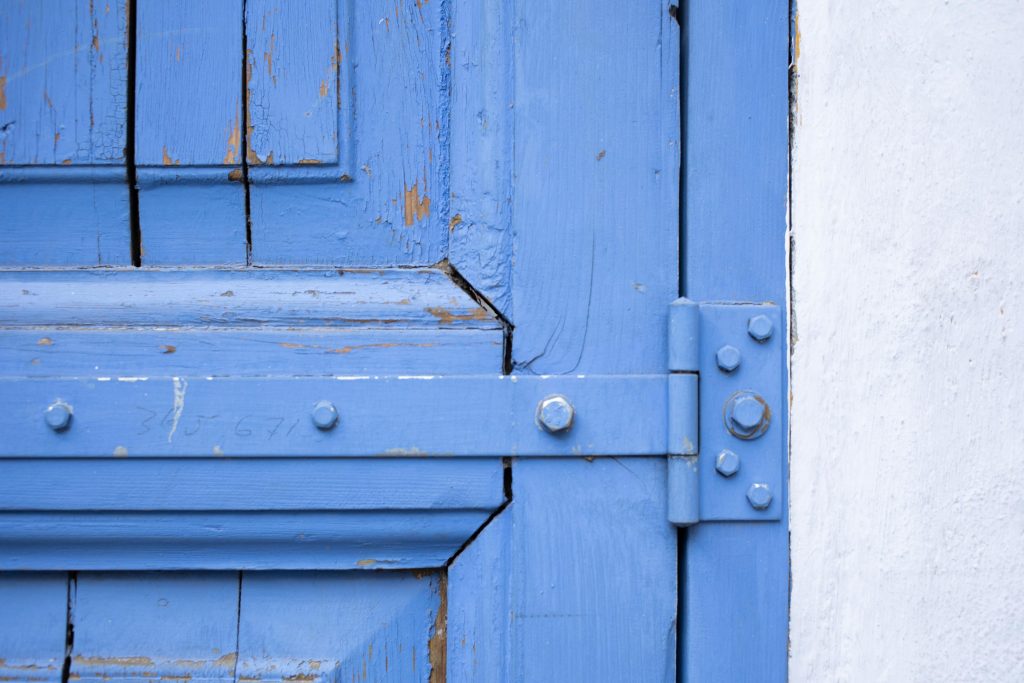
Conclusion
Expansion joints are silent guardians of structural health, quietly absorbing movements that would otherwise lead to costly damage and safety hazards. By understanding material behavior, movement types, and installation techniques, engineers and builders can specify the right joint for every application—ensuring resilience, durability, and peace of mind. Next time you cross a bridge, walk down a long hallway, or inspect piping, take a moment to appreciate these engineered cushions that keep our built environment flexible and robust.
Post Comment