Can MDF Be Used for Load-Bearing Walls?
Introduction
When planning a renovation or new build, you may be tempted to use medium-density fiberboard (MDF) for everything—from cabinets to wall panels. MDF’s smooth surface, low cost, and ease of machining make it a go-to material for interior finishes. But can MDF safely replace traditional framing components in load-bearing walls? In this post, we’ll dive into the structural properties of MDF, explain why it’s unsuitable for bearing heavy loads, and explore the right materials and construction methods for strong, code-compliant load-bearing walls. Whether you’re a DIY enthusiast or a budding contractor, you’ll come away with clear guidelines and best practices for building walls that stand the test of time.
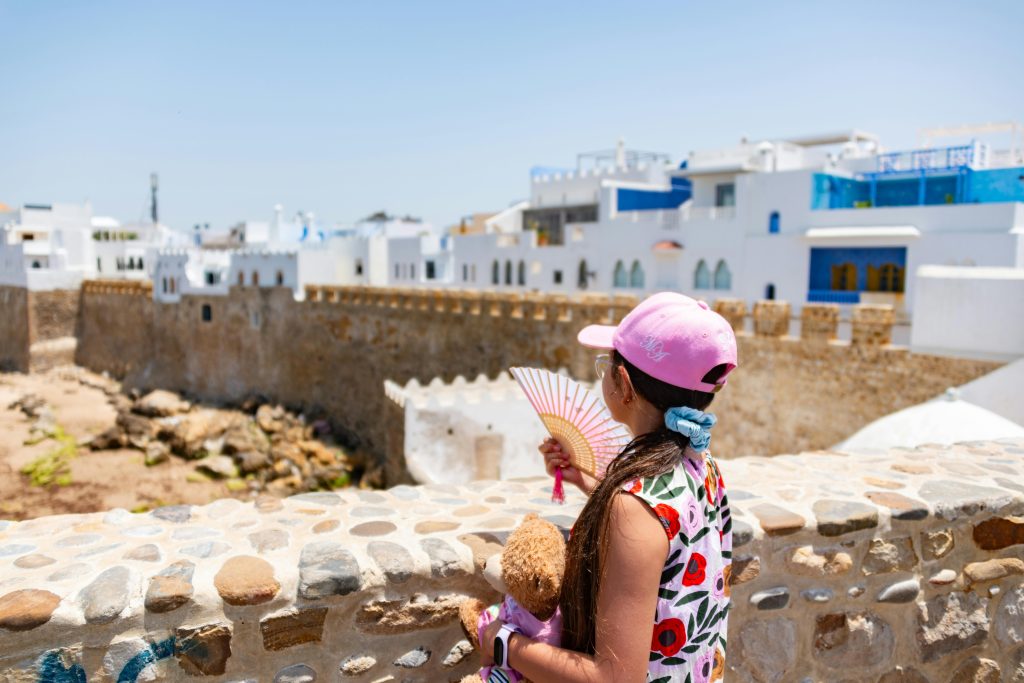
Understanding MDF: What It Is and Isn’t
What Is MDF?
- Composition: Wood fibers combined with resin and wax, compressed under heat.
- Density: Typically 600–800 kg/m³—denser than particleboard but less than most softwoods.
- Surface Quality: Exceptionally smooth and uniform, ideal for painting and veneers.
Structural Limitations of MDF
- Low Bending Strength: MDF’s modulus of rupture (bending strength) is far below that of framing lumber or plywood.
- Poor Shear Resistance: Without strong internal grain or cross-layers, it can’t resist lateral forces.
- Moisture Sensitivity: Swells, softens, and delaminates when exposed to humidity or water.
- Fastener Pull-Out: Screws and nails can strip out under load, compromising connections over time.
Why Load-Bearing Walls Need Structural Materials
Load-bearing walls transfer weight from above—floors, roofs, and sometimes other walls—down to the foundation. For safety and longevity, these walls must satisfy three main requirements:
- High Compressive Strength
- The ability to bear vertical loads without crushing or buckling.
- Lumber studs (e.g., 2×4 or 2×6) and engineered beams (LVL, glulam) are designed for these forces.
- Shear Resistance and Lateral Stability
- Walls must resist wind loads, seismic activity, and racking.
- Structural sheathing (plywood or OSB) and plywood diaphragms tie studs together to form a rigid frame.
- Reliable Fastening
- Framing members must hold nails, screws, and metal connectors securely over decades.
- Building codes mandate minimum fastener schedules and material grades.
MDF fails on all three counts: it crushes under high loads, warps under lateral pressures, and loses grip on fasteners in long-term use.
Comparing MDF to Structural Alternatives
Property | MDF | Softwood Lumber (e.g., SPF) | Plywood/OSB | Engineered Lumber (LVL) |
---|---|---|---|---|
Compressive Strength | Low | High | Moderate | Very high |
Modulus of Rupture (MOR) | ~20–30 MPa | ~40–90 MPa | ~30–60 MPa | ~35–80 MPa |
Shear Strength | Poor | Moderate | High (cross-laminated) | High |
Moisture Resistance | Very poor | Variable (depends on grade) | Good (exterior grade) | Good (resists warping) |
Fastener Holding | Low | High | Moderate | High |
Key takeaway: While MDF shines in cabinetry and decorative trim, structural framing requires materials specifically engineered to handle load, moisture, and fasteners under stress.
Building a Safe, Load-Bearing Wall: Step by Step
1. Framing with Dimensional Lumber
- Select Stud Size and Spacing: Commonly 2×4 or 2×6 studs, spaced 16″ on center for standard residential walls.
- Use Grade-Stamped Lumber: Look for “SPF” (spruce-pine-fir) or similar, with visible grade stamps indicating structural rating.
- Install Top and Bottom Plates: Anchor bottom plates to the foundation with anchor bolts; secure top plates to ceiling joists or beams.
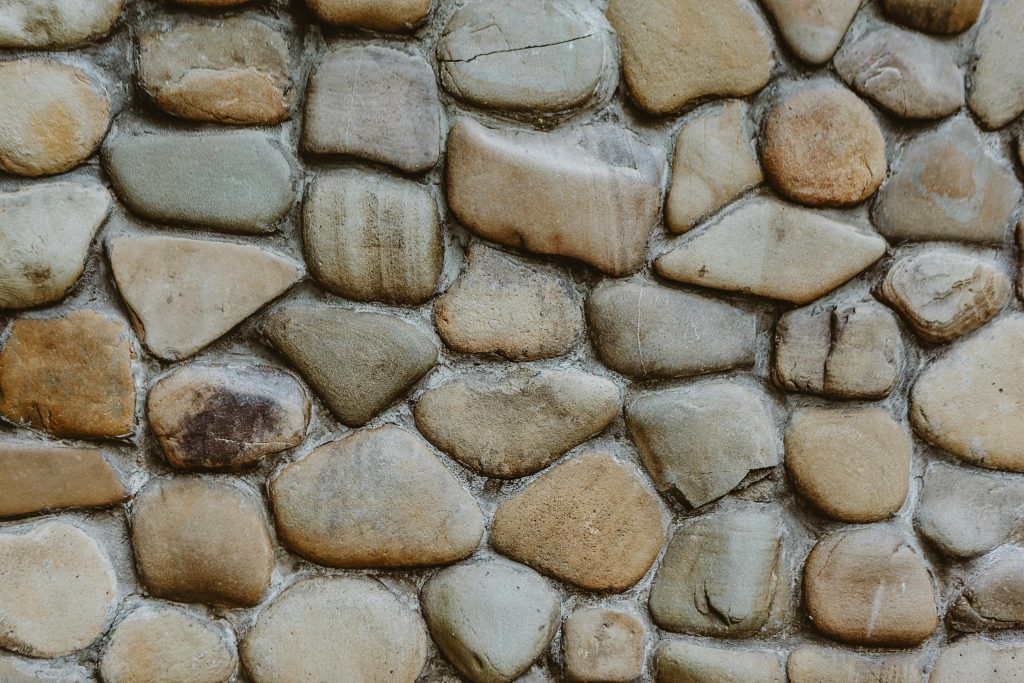
2. Applying Structural Sheathing
- Plywood (APA Rated): Exterior-grade, 5/16″–3/8″ minimum thickness for shear walls.
- Oriented Strand Board (OSB): Often more cost-effective; 7/16″–1/2″ thickness typical.
- Installation Tips: Stagger panel joints, nail or screw per code schedule, and seal gaps against moisture.
3. Integrating Engineered Members (Optional)
For longer spans or heavy loads (e.g., above large openings or on multi-story builds), consider:
- LVL (Laminated Veneer Lumber): High uniform strength, excellent for headers and beams.
- Glulam Beams: Curved or straight beams made from glued wood laminations—ideal for open floor plans.
- I-Joists: Engineered for floor and roof joists with high stiffness and low weight.
4. Adding Non-Structural MDF Finishes
Once your structural frame is sound, you can leverage MDF’s aesthetic advantages:
- Interior Wall Paneling: Affix MDF panels over sheathing or ½″ plywood underlayment.
- Built-In Cabinets & Shelving: Secure to studs or blocking, never as a standalone structural support.
- Millwork & Trim: Baseboards, crown molding, and wainscoting—mounted to studs or backer boards.
Real-World Example: Garage Conversion
Imagine you’re converting a standard two-car garage into a home office. The original walls are non-load-bearing, but you decide to remove one garage door and replace it with a framed wall—bearing the roof load. Here’s a sample workflow:
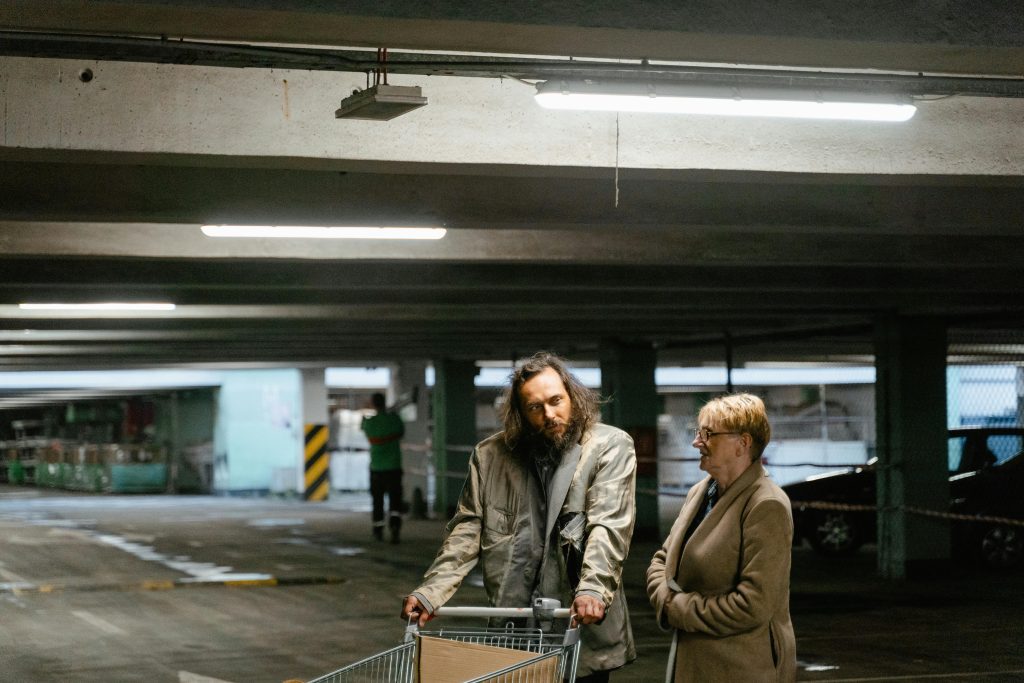
- Assess Loads: Consult an engineer to confirm roof load and any additional floor or attic loads.
- Install Header Beam: Use an LVL header sized per span and load calculations.
- Erect Stud Wall: 2×6 studs at 16″ O.C. tie into header and existing plates.
- Sheath for Shear: Apply ½″ OSB sheathing on the exterior side, nail per code (6″ edges, 12″ field).
- Finish Interior:
- Secure ½″ plywood backer (optional) for point loads (e.g., TV mount).
- Mount ¼″ MDF panels or ⅜″ decorative MDF on top of backer for a smooth painted finish.
Code Compliance and Safety Considerations
- Building Codes: The International Residential Code (IRC) and local amendments specify materials, fasteners, and construction details for load-bearing walls.
- Inspections: Framing and sheathing typically require inspection before drywall or finishes are applied.
- Moisture Barriers: Exterior walls need house wrap and flashing to protect sheathing; interior MDF must stay dry.
- Fire Ratings: Some walls require fire-rated assemblies; MDF does not meet fire-rating standards without additional treatments.
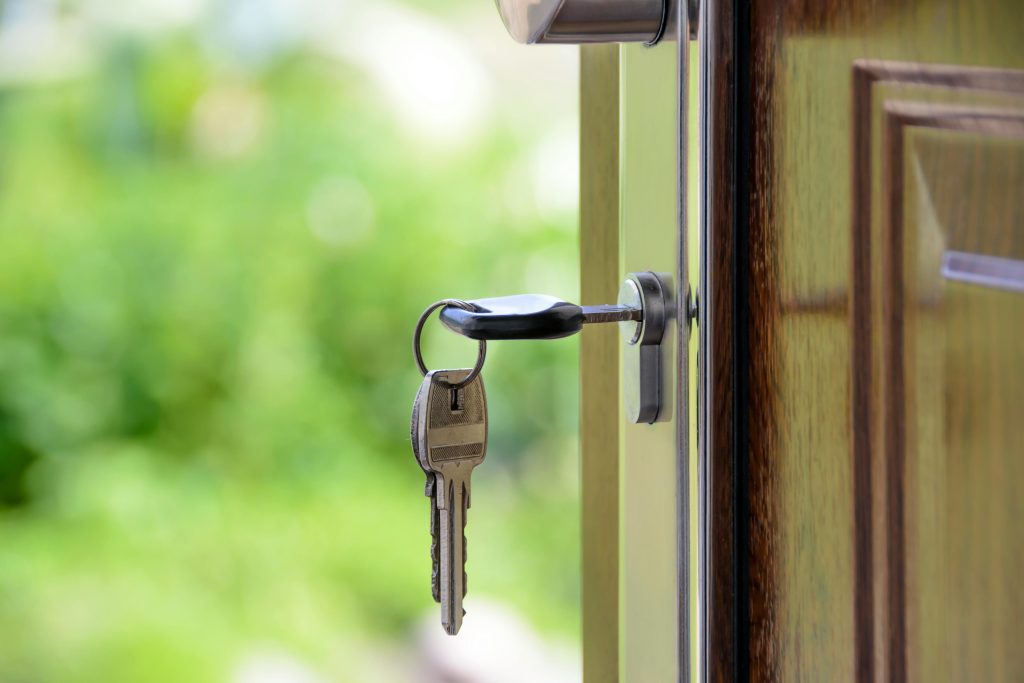
Conclusion
MDF is a fantastic material for interior cabinetry, wall panels, and decorative millwork thanks to its smooth finish and ease of machining. However, its low structural strength, poor moisture resistance, and weak fastener retention make it wholly unsuitable for load-bearing walls. When safety, longevity, and code compliance are on the line, always rely on properly graded dimensional lumber, structural sheathing (plywood or OSB), and engineered beams. Once your wall frame is solid, you can use MDF as a finish layer—never as a substitute for the structural core. By following these guidelines, you’ll ensure your walls stand strong for decades, keeping your home safe and sound.
Post Comment